In a world marked by trade tensions and economic uncertainty, Resonac Graphite Business Unit is redefining its approach to sustainability, innovation, and customer partnerships. Tim Saxon, CMO, reflects on the current challenges as we revisit the company.
LEADERS IN AN EVOLVING ELECTRODE INDUSTRY
Today’s headlines are filled with discussions about tariffs and trade wars, making the future of global commerce a topic of widespread concern.
We reconnect with Resonac Graphite Business Unit (RGBU) to explore how these developments have affected the company since we last spoke a year ago.
“Regardless of the outcomes in the current trade discussions, I believe this period will have a lasting impact on how businesses think about their suppliers, operations, and customers in the future,” introduces Tim Saxon, CMO.
The last year has been challenging for the graphite electrode (GE) industry, with most major competitors finishing 2024 in a financial deficit, and worryingly, Q1 2025 has not seen much improvement.
“Much like the steel producers we serve, we operate in an industry where China manufactures over half of the world’s supply.
“With enough capacity to meet its domestic needs four times over, China exports its ‘subsidized overcapacity’ to other global markets. This puts significant downward pressure on domestic pricing and harms the local suppliers and regions where they operate,” Saxon points out.
Fortunately, various government and trade organizations have begun understanding the need for a healthy domestic electrode industry, as demonstrated by tariffs and anti-dumping duties on Chinese electrodes in the European Union (EU), US, and Japan, which just announced their preliminary duties in February this year.
“80 percent and 75 percent of the total spend of our Japanese and US electrode plants stayed inside the respective countries. These funds will support domestic energy suppliers, local and regional governments in the form of taxes, domestic workers, and the communities where they live,” Saxon explains.
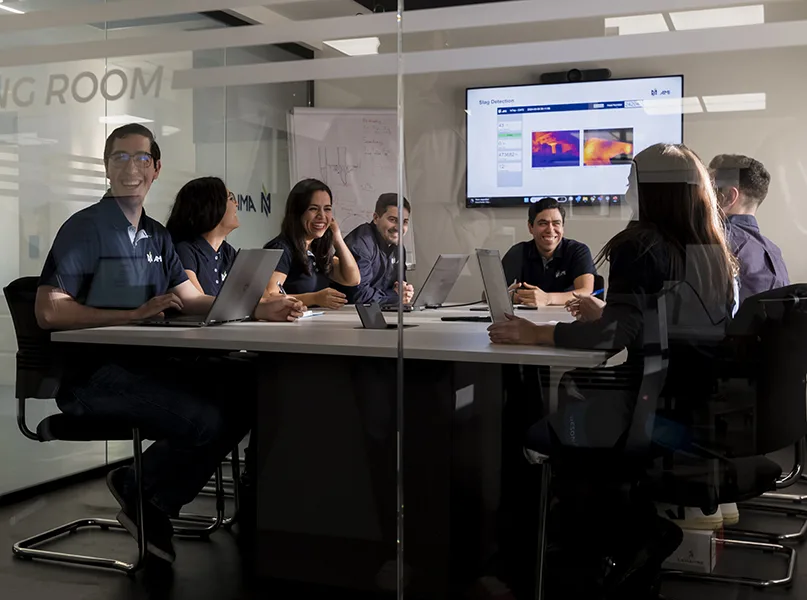
EVER-EVOLVING ELECTRODES
As with all industries, the GE market is continuously evolving, and RGBU primarily services customers who use electric arc furnaces (EAFs) to melt scrap steel into new products, creating 75 percent less carbon dioxide emissions than the traditional blast furnace method of steel production.
One of the many advantages of an EAF is its flexibility and agility. Depending on customer orderbooks, the furnace can run to maximize production volumes or run to maximize efficiency and minimize energy consumption.
“We are very excited to be a critical part of the circular economy, in that our electrodes are essential for this type of steel recycling. It is widely agreed that the future is bright for the EAF industry, and we are glad to be partners with electric steelmakers worldwide,” Saxon enthuses.
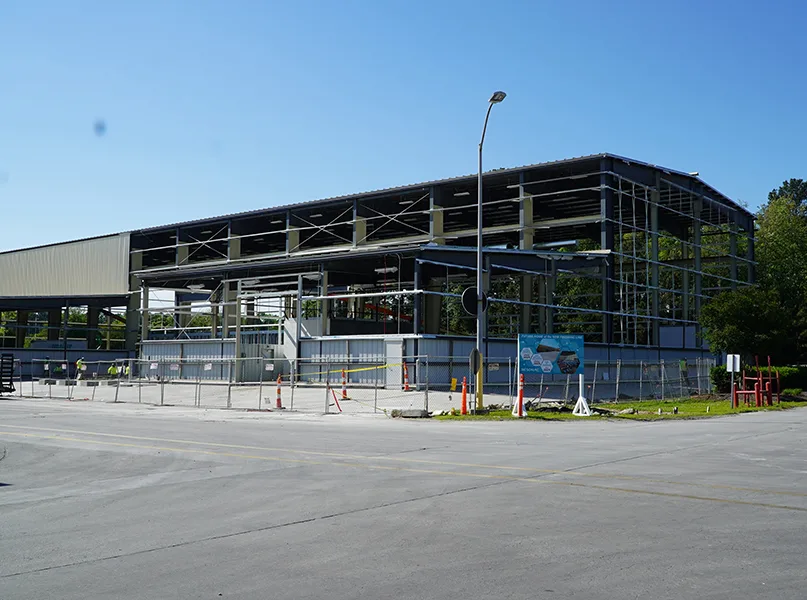
A GE is needed to make every ton of EAF steel, and the product is becoming increasingly commoditized. This is the primary contributor to the current global challenge of balancing supply and demand.
“We are optimistic that the proper authorities are addressing those challenges in places where they are needed most.
“Regardless of the outcomes in trade cases or geopolitical conflicts, we understand our responsibility is to be innovative and continuously add value to our customers’ operations. Like many industries, we believe future success in the steel and GE business is moving toward digitalization and value-added services,” he acknowledges.
Though the electrode is an essential part of melting steel, it is just one instrument in the orchestra that makes up the symphony of an EAF operation. The electrode’s performance is impacted by how the furnace operates, which is ultimately determined by the customer’s needs.
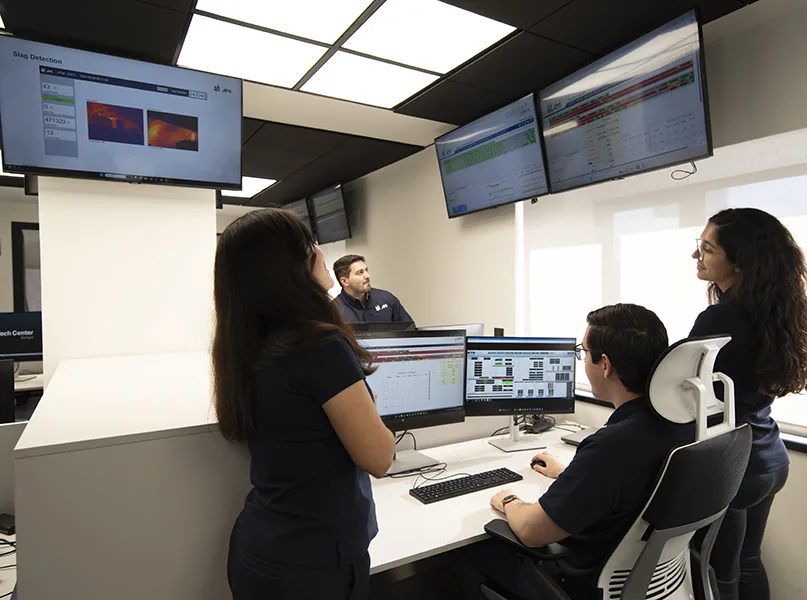
A SYMBIOTIC SYMPHONY
By acquiring AMI Automation (AMI), RGBU can help customers meet their business needs in real time through EAF optimization.
“This acts as a ‘digital conductor’ of the orchestra (the EAF) to achieve the optimum symphony (the EAF performance), with the electrode as the instrument,” Saxon analogizes.
When RGBU acquired AMI, many people viewed it as a paradox that a large, traditional electrode supplier would purchase an innovative technology company known for helping customers reduce their electrode consumption.
“We view our role as a way to serve our steelmaking partners better. As an electrode supplier for 80+ years, we have continually invested in R&D to manufacture the best products on the market. By utilizing AMI’s products and services, our customers can achieve peak performance from their EAF, including the electrode,” Saxon expresses.
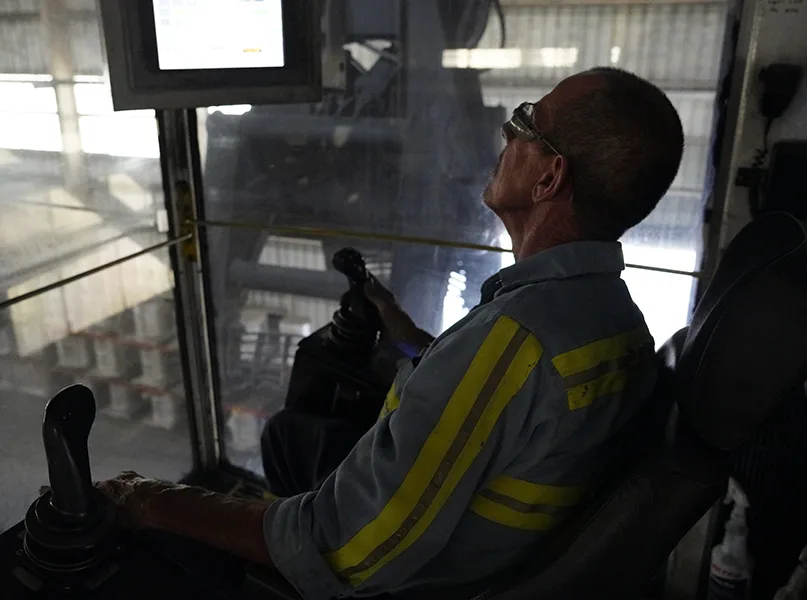
“For decades, RGBU has manufactured premium GEs, but their performance can be hindered by factors unrelated to the electrode in the furnace. Imagine a skilled, first-chair violinist playing a Stradivarius being drowned out by a novice in the back, honking on a cheap trumpet. The true quality of an electrode shines in a fully optimized EAF; thus, we see the RGBU and AMI partnership as a fusion of tradition and innovation.”
Within this partnership, RGBU can now work with customers in other areas such as employee safety, supply chain management, and decarbonization.
Through collaborating with RGBU, AMI has additionally developed digital tools designed to detect potential issues with the furnace and electrodes.
These early warning indicators not only allow the furnace crew to react and mitigate issues but also provide an opportunity to clear the furnace floor, ensuring the safety of operators.
“We view our role as a way to serve our steelmaking partners better. As an electrode supplier for 80+ years, we have continually invested in R&D to manufacture the best products on the market”
Tim Saxon, CMO, Resonac Graphite Business Unit
TRANSITIONING TO A NEW MARKET
After laying out a prudent and measured approach, RGBU has entered the electric vehicle (EV) battery business through its pilot plant in Spain.
While the GE and EV battery industries rely on synthetic graphite, they have different views on global supply and demand. The latter in particular recognizes the strategic importance of graphite and is taking steps to reduce dependence on one region.
The EU and US classify graphite as a critical mineral essential for modern technologies and national security. In contrast to the locally rooted global steel and GE industries, which have consolidated over decades with over half of production in China, the EV battery market has rapidly expanded due to surging demand for EVs and synthetic graphite.
“The early, long-term projections for EVs resembled a modern-day gold rush, and China had the resources, capacity, and economic environment that allowed it to become the dominant supplier, producing 97 percent of the world’s battery anode materials by 2018,” Saxon comments.
As the COVID-19 pandemic exacerbated geopolitical stability and supply chain resiliency, EV battery producers began diversifying their supplier base, particularly in the US and Europe, with the optimistic growth forecast suddenly leading to the same artificial gold rush in these regions.
“The projections for EVs have softened a bit, but at RGBU, we are not necessarily disappointed. We had a plan from the beginning and are taking a prudent, measured approach to that market. This softening could benefit us because we are not overleveraged while implementing our plan,” he reports.
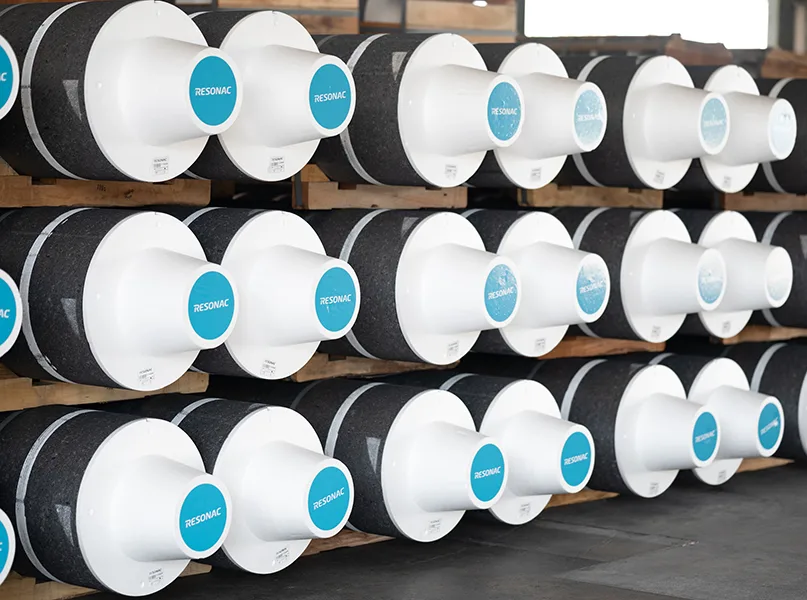
GREEN AND CLEAN
As a Resonac company, RGBU prioritizes environmental considerations and decarbonization in its mission to “change society through the power of chemistry.”
“We harness the power of graphite to enhance societal well-being by enabling steel recycling with our GEs and supplying graphite for renewable energy storage in batteries,” urges Saxon.
It’s crucial for RGBU to differentiate between sustainability and decarbonization; the latter focuses on production processes and emissions, while the company highlights the significance of environmental, social, and governance (ESG) factors.
“Our employees are our foundation, and we are committed to fostering a safe, supportive workplace for their growth. ESG is not just part of our strategy; it is our strategy. We are dedicated to continuously improving, lowering our carbon footprint, and ensuring a resilient supply chain,” he highlights.
“Long before it was trendy, our plants in Austria and Japan utilized renewable energy from hydropower, and our facility in A Coruña, Spain invested in local wind energy.”
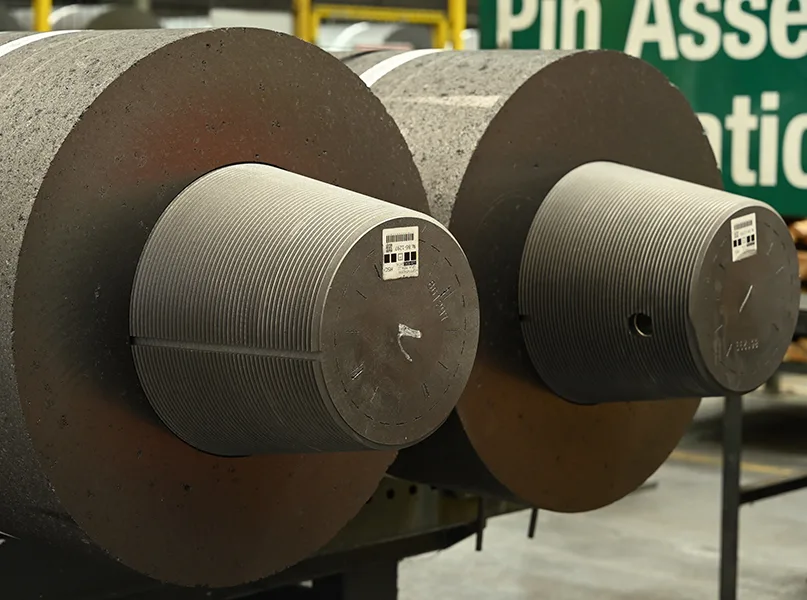
At the inaugural Global Steel Climate Council® Member Forum in Brussels, Belgium, discussions around green steel highlighted the need for clear definitions and the complexities of monetizing sustainable products.
“It’s evident that the future is green, yet the term is overused. Therefore, manufacturers must scrutinize investments carefully,” Saxon warns.
Indeed, while many support clean products, real investments require consumer willingness to contribute to the extra expense, or they just end up benefiting less responsible players.
“Decarbonization is more of a regional than a global effort. We anticipate that supplying a GE with an Environmental Product Declaration (EPD) will soon be as standard as providing a safety data sheet, and RGBU is ready for this shift,” he states optimistically.
“Our employees are our foundation, and we are committed to fostering a safe, supportive workplace for their growth. ESG is not just part of our strategy; it is our strategy”
Tim Saxon, CMO, Resonac Graphite Business Unit
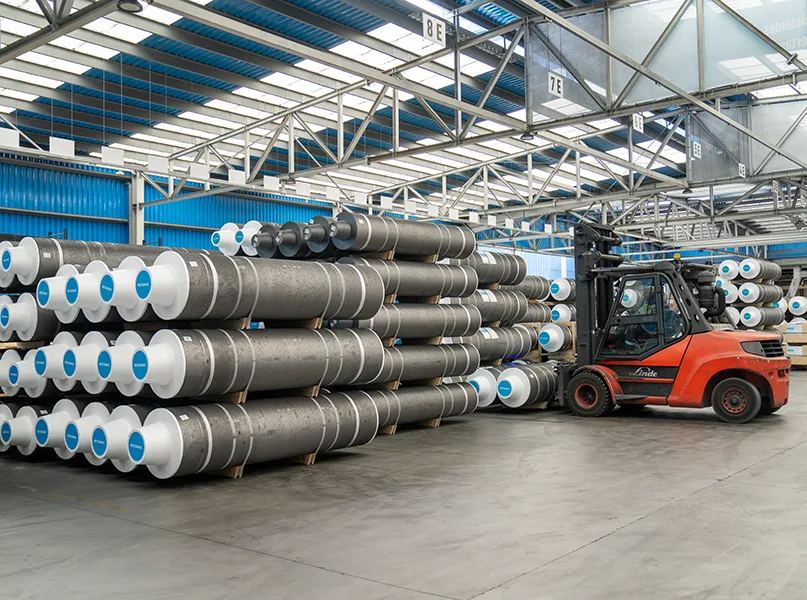
ENHANCING MARKET OPPORTUNITIES
An area where RGBU has wisely invested in its future is its Ridgeville location in the US, where a new, state-of-the-art GE machining line is set to be operational this summer.
This investment focused on the challenges of the US steel industry, hinging on the need for precisely-machined electrodes for new EAF furnaces.
“The project utilized US-made steel, ensuring the same customers using these electrodes to turn scrap steel into building materials were involved in creating the structure that machines them,” Saxon observes.
Recognizing the complexities of modern EAF steelmaking and having the country’s newest advanced electrode machining line, alongside cutting-edge EAFs, will ensure RGBU remains the benchmark of the US steel industry.
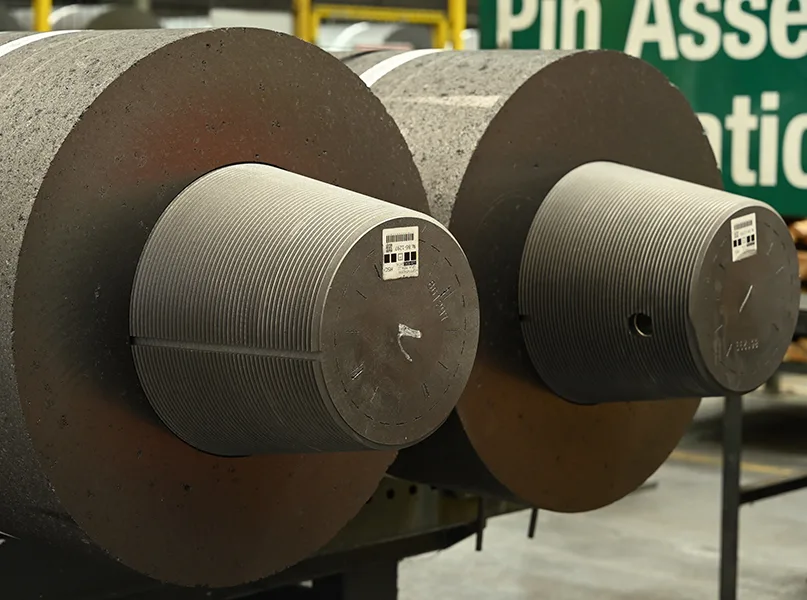
“Considering the current state of our industry, our priorities for the coming year are straightforward. We aim to establish ourselves as a responsible and respected leader in the synthetic graphite sector,” he impassions.
“While factors such as critical mineral designations, regional outlooks, tariffs, anti-dumping duties, and unfair competition are relevant to our industry, it is essential to understand that these issues alone will not make us a true leader.”
With this in mind, RGBU is committed to being the supplier of choice in synthetic graphite by delivering maximum value for its customers and aiding them in challenging business environments by striving to offer competitive products and services, ensuring sustainability and value in the marketplace.
“Looking ahead, we aim to keep our business sustainable for our colleagues, customers, suppliers, and stakeholders. This involves being economically, environmentally, and managerially sustainable while upholding our core values – these are our priorities for the future,” Saxon concludes.