Saving lives since 1946, Martin-Baker has honed a unique set of ejection seat capabilities that are at the cutting-edge of aircraft safety. Mark Cooper, Vice President of Sourcing, delves into the company’s commitment to technological and operational excellence.
SAFETY WHEN IT MATTERS MOST
Due to ongoing geopolitical conflicts, nations around the world are increasingly turning their attention to defence equipment procurement and operational availability, making it both a fascinating and challenging time to operate in the aerospace manufacturing sector.
As a result, organisations across the industry are working hard to develop capabilities and processes that respond and deliver products with shorter lead times and increased rates. However, the innovation needed to achieve these capacities and stay ahead of global conflicts means that manufacturing development cycles are under considerable pressure.
On top of this, defence budgets continue to tighten following successive international economic challenges, which is pushing the industry towards more cost-efficient solutions.
“All these are central to defence sector procurement, and we are constantly working to optimise the quality, cost, and delivery performance using technology and supply chain improvements,” introduces Mark Cooper, Vice President of Sourcing at Martin-Baker, the world’s leading manufacturer and supplier of ejection seats.
“Our job is now significantly more complex and challenging than it was five years ago, but my team has shown multiple times that they can rise to ever higher levels and mitigate crises whilst also driving improvement,” he adds.
INNOVATIVE AND LONG-LASTING
Operating at the forefront of the seat ejection subsector, Martin-Baker is proud to support the global aerospace industry with cutting-edge products that have helped save over 7,700 lives and counting.
“A passion for the life-saving nature of the job that we do runs through the business, it’s what grounds you when you are having a bad day and boosts you when you see the reports of successful ejections,” Cooper reflects.
The company supports over 60 aircraft across 106 operators in 85 countries, offering a range of seats that are both innovative and long-lasting. Accompanied by a strong team of experts in the field, Martin-Baker retains the knowledge and skills required to develop complex integrated escape systems.
Furthermore, its status as a family-owned and operated company, which is rare for a business of its size, is a key driver of Martin-Baker’s strong position.
Its role as an ejection seat frontrunner is further upheld by the company’s significant investment in technology and processes, strategically making decisions that have an impact over decades.
“Our ultra-long-term thinking helps us keep focused on sustainable strategies and approaches rather than chasing short-term tactics,” Cooper affirms.
Case in point, Martin-Baker recently recorded an ejection from a product over 40 years old, demonstrating the longevity of a seat in service.
The company also aims to control the intellectual property (IP) and manufacturing expertise of its solutions by developing in-house capabilities that ensure it serves its customers for as long as they are flying.
Additionally admirable is the strength of Martin-Baker’s supply chain and the part it has played over the last few decades. As such, the combination of a diverse network of suppliers and extensive internal capabilities is a key component of the company’s success and resilience.
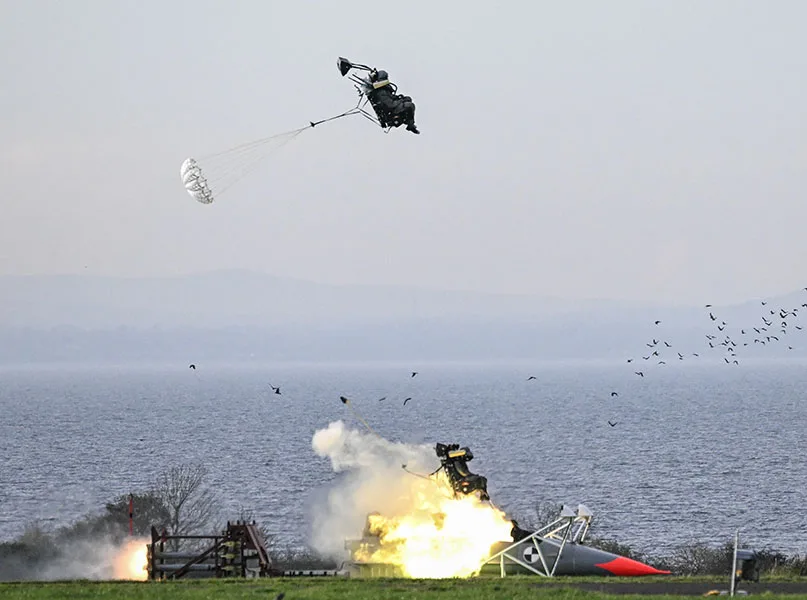
AT THE FOREFRONT OF AIRCRAFT SAFETY
Martin-Baker has developed an enviable reputation for state-of-the-art equipment and manufacturing capabilities, which call for significant investment and capital expenditure (CapEx).
“Our products can be extremely complex and are designed at the limits of technology, so our strategy is to control manufacturing know-how to ensure we support our customers long into the future,” Cooper assures.
The COVID-19 pandemic and the subsequent energy crisis highlighted a need for the company’s long-term strategy, as the increased obsolescence issues faced by customers in recent years reinforce the resilience of Martin-Baker’s products.
On account of this, the company’s factory is capable of manufacturing almost any part of the ejection seat, brought about by significant and thoughtful investments.
Martin-Baker also firmly believes in offering the highest quality product at the most competitive price point, which consequently drives its investment in the latest technology, most recently demonstrated by the acquisition of computer numerical control (CNC) machining cells and cartridge assembly lines.
“We have a factory deployed with the latest milling and turning centres and have also invested in automated inspection and verification with vision systems and computed tomography (CT) scanning to aid equipment inspectors and eliminate defects,” Cooper expands.
The company’s latest technological investments go hand-in-hand with Martin-Baker’s commitment to safety.
“Product safety is our core focus and guiding principle. The ejection seat is the last line of defence in the event of aircraft failure. Although it sits dormant for many years, the seat must be operational when needed,” he asserts.
With this in mind, the company regularly conducts quality assurance (QA) and quality check (QC) processes for the business and its supply chain.
In the last two years, Martin-Baker has additionally been initiating and driving a zero-defects culture throughout its supply chain, in aid of its product safety goals.
“This seeks to create openness and transparency in terms of supplier defects so that we can collaborate on preventative solutions,” Cooper adds.
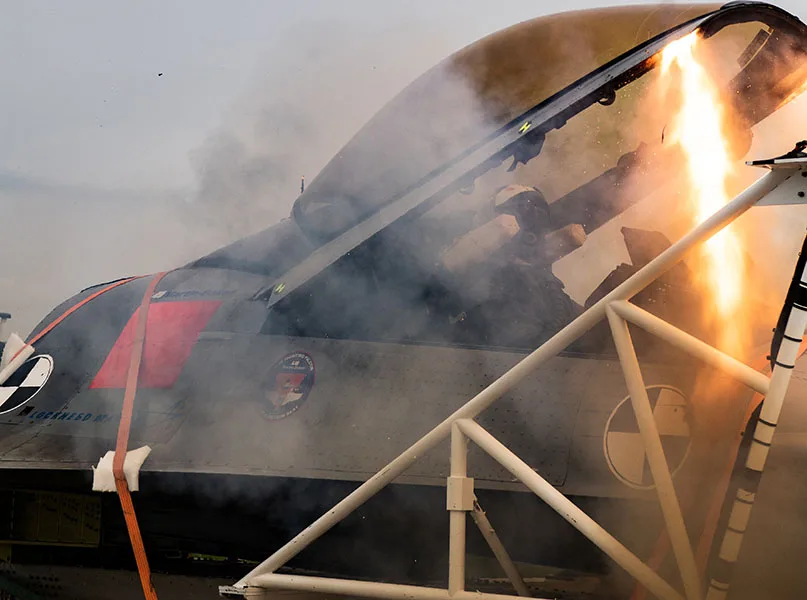
PASSIONATE AND SKILFUL
Alongside its operational safety targets, Martin-Baker is further committed to investing in its people.
“Personally speaking, I believe that the core asset of any business is a strong team, and we work very hard to create a company where people are engaged,” Cooper reflects.
Indeed, employee development and recognition are important for the retention of staff and therefore the business, whether that is developing competence within its roles to improve employee efficiency, or through promotions.
Martin-Baker’s strong company-wide dedication to improvement is exemplified by the recent restructuring of Cooper’s team to create more specialised management roles, facilitate progression routes, and introduce early career pathways.
Martin-Baker also strives to promote internally before reaching out to external applicants.
“We do this for two key reasons; firstly, it is a complex and unique business where the learning curve as an external hire is steep. Secondly, we want to reward our existing staff for high performance.
“I have been lucky enough to experience this and see various areas of the business, and this is a common theme through them all,” he reminisces.
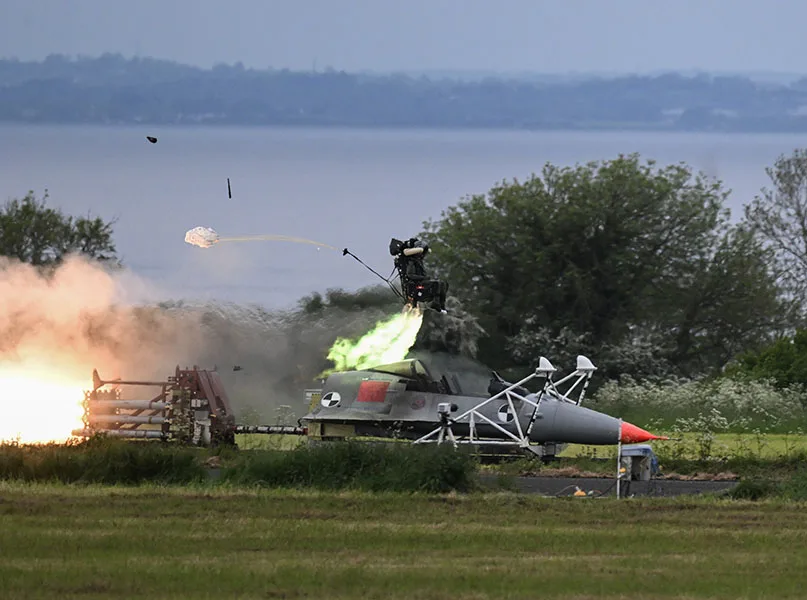
Indeed, Cooper has enjoyed a diverse array of roles at Martin-Baker, including positions in production engineering, procurement, factory management, and environmental testing, highlighting how the organisation encourages career development across its departments.
“Throughout my time with the company, I have been privileged to work with excellent people, and within my role of Vice President of Sourcing, I have inherited a fantastic team who are highly capable and engaged.”
Looking ahead, Martin-Baker is focused on continuously improving its product quality whilst ensuring its on-time delivery fully recovers following recent global and national events such as the pandemic and energy crisis.
As such, its priorities remain on operational resilience, safety, and staff engagement, which filter across the entire business.
“We have made really great progress over the last year through a lot of hard work and determination, and we will push for even better in the future.
“There are some risks on the horizon with tariffs and trade complications, so managing and mitigating these will become a growing part of our roles over this year,” Cooper concludes.