With manufacturing set to spend more on digital transformation than any other industry, we speak to Simon Culshaw, VP Manufacturing Northern Europe at Atos to find out what it means for the industry.
INFORMATION TRANSFORMATION WITH ATOS
The pace of change across the manufacturing sector is starting to increase. With the evolution to more customer-centric and service-centric business models, it is imperative that manufacturers make better use of the data and technology available.
The manufacturers that invest in this now will get ahead of the curve, see stronger returns and will best equip their businesses to flourish in the future. The future of manufacturing, therefore, lies in maximising the effective use of both information and operational technology (IT and OT). By digitising value chains, manufacturers will be able to join up their businesses, optimise demand and supply and create the agility needed to respond to changing market dynamics.
As a world leader in IT solutions, cybersecurity and decarbonisation services, Atos provides end-to-end solutions for all industries. Its performance enhancing services for manufacturing span both IT and OT and are enabling new production possibilities, more sustainable supply chains and factories, and growing revenue streams. IT plays a significant role in today’s business world, and when integrated effectively into OT, has the potential to improve manufacturing and create new business models in ways that are still to be discovered.
“Adopting an end-to-end approach to smart manufacturing and IT/OT integration has the ability to link up businesses that operate in silos and drive real, sustainable business value,” Simon Culshaw, VP Manufacturing Northern Europe, Atos tells us.
Culshaw suggests that looking at manufacturing operations in the context of the wider business is needed in order to maximise return from smart manufacturing / industry 4.0 initiatives. “You can improve manufacturing efficiency or reduce waste from operations, but such initiatives create even greater value if they are, for example, linked through to procurement and planning. This can, along with other benefits, free up working capital, eliminate the need for spot buying, prevent starvation events and enable just in time delivery.”
Reduced waste and energy consumption along with increased efficiency will contribute to net zero targets as well as adding to the bottom line, and Culshaw recognises that it is important to factor these benefits in when implementing smart manufacturing solutions. The use of technology to enable these benefits is changing how businesses operate and paving the way for new business models.
“Technology has the ability to move manufacturing businesses from making to stock to making to order, from making in specific factories to design anywhere, build anywhere and from pure manufacturing companies to companies that add further value through services and direct customer relationships,” says Culshaw.
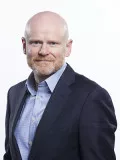
“I am starting to see change in the market with more manufacturers committing to scale up smart manufacturing initiatives. The Director of IT at a large food manufacturer told me recently that the only thing he would have done differently with their Industry 4.0 initiative is to do it much more quickly and at scale”
Simon Culshaw, Manufacturing Director, Atos
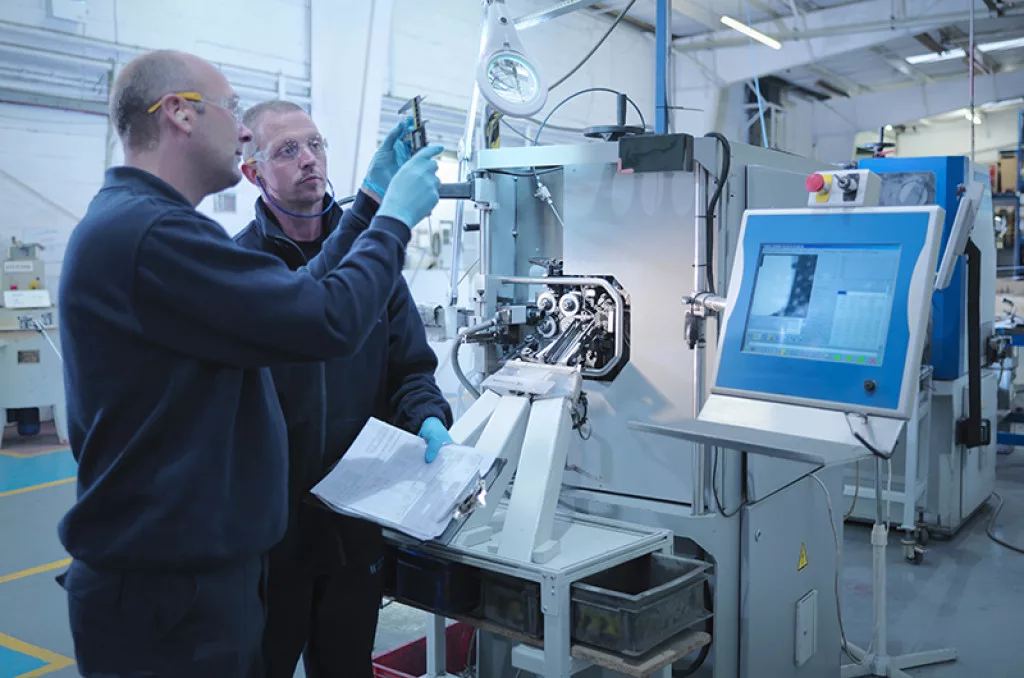
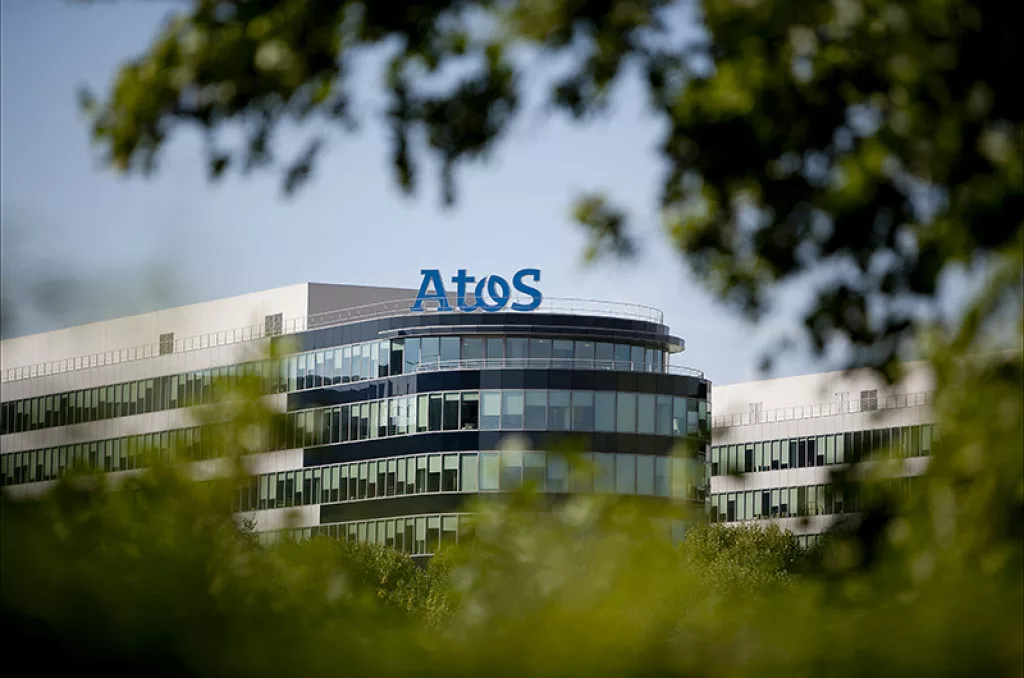
OPPORTUNITIES AND POSSIBILITIES
As a leader in the digital transformation of manufacturing, Atos builds, implements and operates end-to-end solutions for smarter factories. It is a field that Culshaw himself had already experienced earlier on in his career when he was exposed to manufacturing processes in the pharmaceutical industry.
Although this sparked his interest, it was a while before he got to work in this area in earnest. In the interim, he worked across a number of different industry sectors – experience which has been invaluable in seeing the art of the possible and in generating ideas to be used in a manufacturing context.
“For example, I worked in the telco sector, implementing fully integrated operational support systems (OSS) and business support systems (BSS) which enabled complete zero-touch, automated solutions,” Culshaw elaborates. “It gave me a valuable insight into what was possible with technology and how to run a business based on it.”
Culshaw first became interested in smart manufacturing and the possibilities of digital transformation in the industry through a contact — the IT director at a large food manufacturing company in the UK. Again, the process flowed back to adding to the bottom line.
“He had a vision on how to use technology to improve manufacturing efficiency and reduce waste but was struggling to make the business case for it,” recalls Culshaw. “We met through a conversation about SAP implementation, and he thought they could be doing a lot more integrating this with technology in the manufacturing space.”
The key support processes across the business were run through SAP, such as procurement, accounts payable/receivable, goods in, logistics, production planning and demand planning. They each had visibility in the business, but as Culshaw explains, “In the middle of all that was the big black box which is manufacturing. This is how the business viewed their factories. They can see what goes into them and they can see what comes out of it, but they have no idea what happens inside.”
Using technology to control the manufacturing process, the product lifecycle and to integrate these into the rest of the business enables you to gain control over the end-to-end supply chain. In this case, Culshaw’s contact needed a business case that would bring it to life.
It was this opportunity and the subsequent implementation to deliver the business case that resulted in Culshaw’s fascination with the possibilities of technology in the manufacturing context.
“These solutions were not difficult to implement, but for me they were quite ground-breaking, especially when they were integrated into end-to-end business processes,” says Culshaw. “In terms of the technology used in the factory, it was generally standalone to that point, and this bought manufacturing processes into the mainstream business.”
“Atos aims to be a leader in smart manufacturing services which drive sustainable business value through the implementation of intelligent, integrated solutions. These solutions transform manufacturing by connecting business strategy, people, processes and technology”
Simon Culshaw, Manufacturing Director, Atos
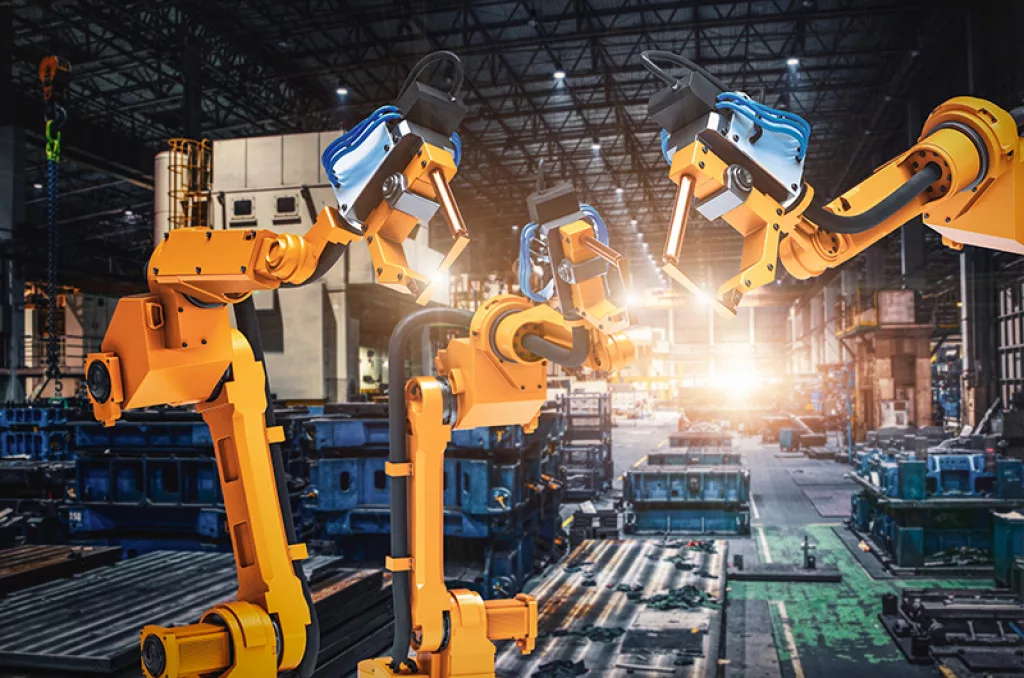
INNOVATIONS IN MANUFACTURING
As an example of the benefits that can be delivered from fully integrated smart manufacturing solutions, Culshaw cites a soft drink manufacturer which he worked with.
They implemented technology to create integrated processes across core business functions, aligning order intake to procurement, goods-in, accounts payable, capacity planning, production scheduling, quality and recipe management, warehouse management, manufacturing control and providing a full product genealogy.
“It enabled the company to achieve 100 percent first-time right in its ingredients processing, provided an accurate picture of stock and enabled effective first-in, first-out routines,” he explains.
The whole approach was driven by looking at the end-to-end manufacturing process and the processes that support it.
“We went on at the soft-drinks manufacturer to implement many more solutions based on a common platform. One such solution drove a significant increase overall equipment efficiency in the plants. It was a solution based on the theory of constraints that enabled them to course correct in real time and maximise yield from the lines,” Culshaw adds.
TRANSFORMING WAYS FOR FUTURE DAYS
Forecasts predict that by 2025, some USD$815 billion will be spent on digital transformation by the manufacturing industry.
“There is a good reason that manufacturing is the industry sector that will have the largest spend on digital transformation. Too many factories are not yet integrated into the business and are still being run on paper and spreadsheets,” Culshaw says.
“Where manufacturing is digitised, there tends to be multiple standalone point solutions that have been put in place to address specific challenges. The cost to the business may be initially low, but the lack of common platforms and integration actually costs the business more and misses the opportunity to drive greater value from the investment.”
Since initiating the smart manufacturing programme at Atos in the UK, Culshaw continues to drive its progress.
“We have teams of people all over the world and an amazing community focused on driving real value for manufacturers from the use of smart manufacturing technology. I have helped drive this in the UK and Northern Europe; it is a real passion of mine and something that I can see enormous potential for across our customer base in the manufacturing sector.”
Looking towards the future, Culshaw has a key objective for 2023.
“Atos aims to be a leader in smart manufacturing services which drive sustainable business value through the implementation of intelligent, integrated solutions,” said Culshaw. “These solutions can transform manufacturing by connecting business strategy, people, processes and technology.”
He goes on to add, “strong partnerships will be the key, and I am keen to be involved in initiatives in this area, as they can help deliver at scale and have the potential to dramatically accelerate time to benefit.”
Nevertheless, when it comes to scaling up smart factories, it is not without its challenges, he warns. Francesco Betti, Industry 4.0 lead for the World Economic Forum and Enno do Boer, lead partner for Industry 4.0 at McKinsey, refer to many manufacturing businesses as being stuck in ‘pilot purgatory’ when it comes to Industry 4.0 initiatives.
“The big challenge for manufacturers is to escape pilot purgatory and to do this at scale,” says Culshaw. “Only by doing so will they make substantial change to the bottom line, increase agility and make the adoption of new business models possible.
“The way in which many manufacturing businesses are run make it difficult to scale Industry 4.0 initiatives. Investment which cuts across business functions and brings the silos together needs active championing at the board level, often from the CEO. This requires a bit of a leap of faith, and there is a nervousness to commit to the benefits that can be delivered.
“A robust business case is often not sufficient, we need to see more active promotion of shining examples of excellence, an ecosystem which enables joint investment and leadership in manufacturing which is prepared to push boundaries. At Atos, we are committed to pushing this and to helping industry move into the modern age of production.”
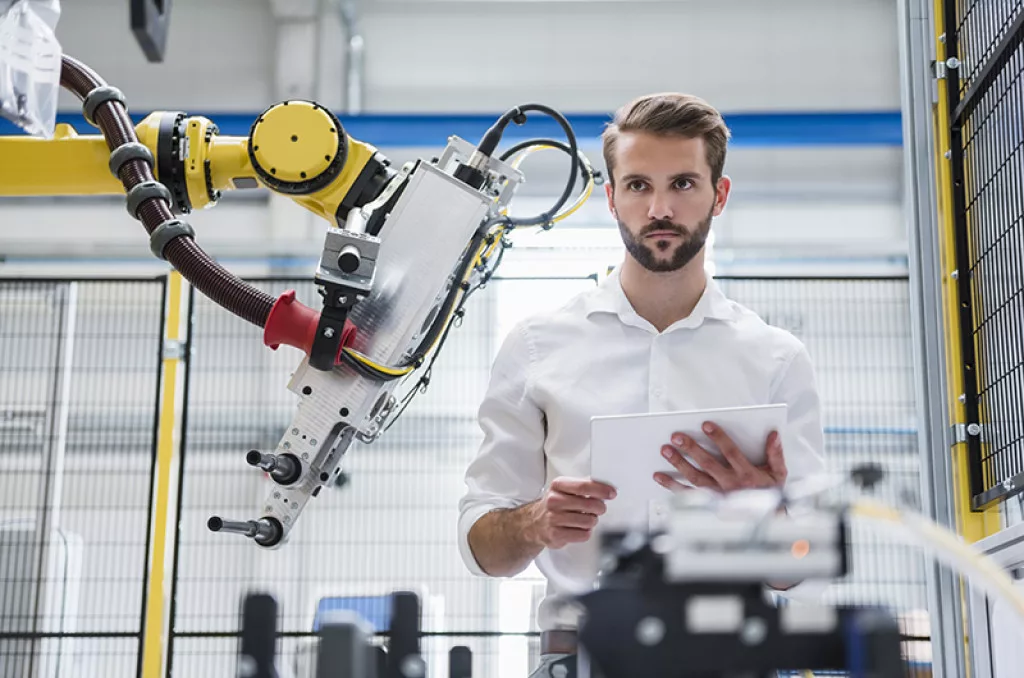